Our Composting Site
One of the cornerstones of EcoVerde’s mission is to select small, “satellite” sites on which to support an agricultural land use while being close to the generators of the relatively innocuous sources for our “recipe.” This increases efficiencies, allows us to use smaller equipment as part of our process, and enables us to tightly control the outcome in our finished products.
Our first such site is located on the Carr Farm on Blakeley Road in East Aurora. The land was once farmed years ago, but we are assisting the Carr Family to bring the farm into a Certified Organic Farm enterprise through sharing labor, equipment and attachments; providing a long-term lease arrangement; and an income stream from a modest payment on the compost we market.
The Farm

When we first began working the farm in the summer and fall 2017, we brush hogged the areas most suited for production and crops, as well as field composting.
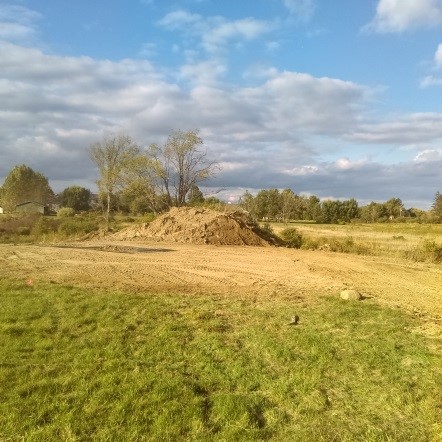
As a part of that process, we utilized a pile of clay spoils on the farm to set up staging areas that are properly pitched, so as to have no direct loss of phosphorus or other nutrients to water courses and ditches.
We then layered gravel and stone to keep the surface dry and navigable, saving erosion and soil degradation. Yes, it was noisy at times, and we had to work long days – and some big trucks brought in stone and gravel – but that work is pretty much completed.

Meanwhile, we began fallow plowing the fields and laying them out for plantings to follow in 2019.
Because the farm will be Certified Organic, we are using fallow till to knock down weeds, get the soil ready for compost applications and small plot research to measure the performance of our organic soil amendments.

The Hoophouse
The Carrs constructed a hoophouse a few years ago, and during spring 2018, we made improvements and set the house up for benches and raised earthen beds to not only test our products, but to also produce a marketable group of vegetables, plants and crops which further assist as a generating income stream for the Carrs.
Composting
As part of our partnering with the Carrs, we found the best field location to do some field composting was in the far southwest corner of the open land on the farm. The roughly 7.0 acres are comprised as maintained grasslands and riparian buffers with native species, which are excellent for keeping nutrients on site and for providing wildlife habitat. The field is surrounded by woodlot on three sides, with about 300 feet of riparian (native) brush and marshy land behind the backyard boundaries of the houses along Blakeley Road. The site is approximately 720 feet from Blakeley Road. (Source: linear measurement tool at USDA-Web Soil Survey)

The land is rotated between composting, then cover crops, then production crops before seeding back to perennial grass sod and back to a compost field. This builds and conditions the soil, maintains a good balance of green space, and allows for best management within the soil types, slopes and diversions that exist on the farm.
We use a small compost turner which has many benefits. It helps mature the material faster, reduces anaerobic odors, and lessens the size of the windrows, hence reducing the opportunity for non-point movement of any nutrients off site. We turn every four to 14 days, depending on the weather conditions.

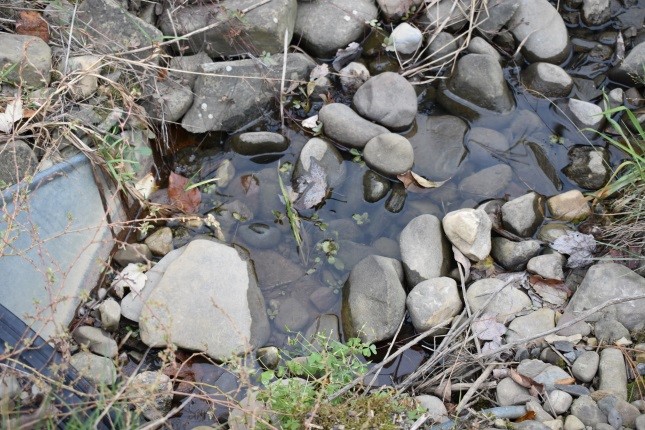
Keeping Clean Water Clean
We continually monitor drainage water for any signs of trouble, and, as you can see, we are keeping our clean water clean (job No. 1 in agriculture). This photo is of the outlet of a culvert under the road before it goes into a marshy, wet area we just maintain in native species.
Windrow Covers
On the right, we use black plastic covers initially when heating the pile to the thermophilic stage. We then use the green compost fleece, which breathes better, to finish them off and maintains an aerobic system. This prevents flies, rodents and odors, and makes for a better end product.
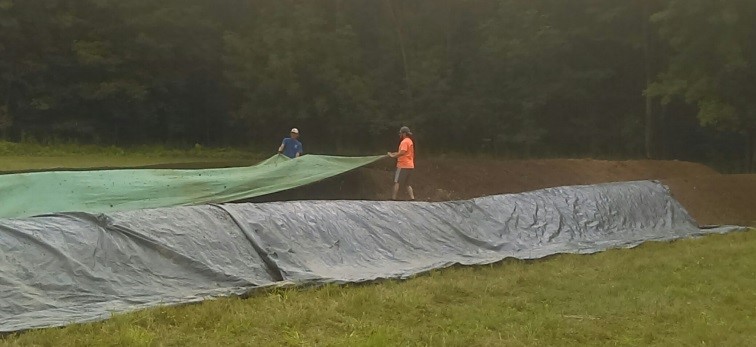

Staging Areas
Once finished, we move the material to a staging area before moving off site for bagging, delivering to customers, or use on the farm.
This small area, designed with the assistance of John Whitney of the USDA/NRCS, is important so as to remove the finished material out of the field.
An important step is to create plenty of buffer to filter out any effluent that might escape the pad (which is rare). NRCS specifications state that an area three times the size of the pad should have a grass or other vegetative filter area. This staging area has five times the area surrounding it seeded to grass, not to mention the minimum of 325 feet of woodlot owned by the Carrs behind it on the west side of the predominant grade direction.

Every step of the site and soil management process – whether on the farm or where we are composting – includes consulting with USDA/NRCS and the Erie County Soil and Water Conservation staff so as to exceed all minimum technical specifications for soil, water and environmental conservation purposes.
The site is registered to NOT EXCEED 3,500 yards. Independent of that threshold set by the DEC, we will likely be less than that with our present throughput rate and as part of our business plan. We need to keep our capacities down so as to maintain the green space and good process quality.
The ‘Ingredients’
The most important part of what we do is to be VERY selective on what we will accept as part of our recipe. We are very selective on what materials we will accept and strictly prohibit any that do not meet our standards.
Manure – Our primary materials that come onto the farm include horse manure, collected from local small farms that don’t have anywhere to put their manure. We’ll often times start working with a farm by removing two to three years’ worth of static piled manure just to clean things up, then we do a regular pickup so as to keep it clean. By having the material fresher from the farm, it supports heat in the compost windrow, which quickly destroys any potentially negative bacteria and significantly reduces weed content.
Food Scraps – Our food waste partners source separate their scraps, typically pre-consumer (in the kitchen). We pick the scraps up in sealed totes, sized to their rate of generation so as to pick up every three to four days and get it into a compost pile as soon as possible. Once in the windrow and being turned, food scraps practically disintegrate into the bulking materials. Food is mostly water, so once in the windrow and turned, it’s hardly discernible and as it moves through the compost cycle, you can’t even tell it’s in there. To date, food scraps have comprised only 5 percent of the total material we are working with – the New York State Department of Environmental Conservation limit is 50 percent. As the project grows, we will not exceed 30 percent, as we think that is the best ratio for our ingredient blend.

This poster is provided to all of our participating restaurants and other food scrap generators.
Some other wastes NEVER accepted include:
• Sewage or septic waste
• Bones or carcasses
• Paper or plastic
• Any garbage other than scraps as indicated
We not only choose to only have these ingredients in consideration of product quality, site management and odors, we are REQUIRED and are closely monitored relative to food waste and total materials brought into the site as part of our NYSDEC Sec. 360 Registration.
Transport & Trucking
Food Scrap Pick-Up Services

We collect our food scraps in appropriately sized, sealed totes using a pickup truck set up with a tailgate lifter.
We pick scraps at three- to four-day intervals, and then use a lifter to place them into a water-tight compactor, as pictured below, to store the food scraps “clean.”
Totes are lifted into a temporary compactor/protainer and stored in small quantities for one to two weeks before being taken to the field for blending with bulking material and set up in a windrow. Once in the field, these windrows are meticulously covered while repetitive turning disintegrates the food within them.
One lesson learned this summer is that we need to take the food scraps to the windrows at a much greater frequency (i.e., immediately). This will significantly reduce providing flies a habitat.

Horse Manure Pick-Up Services
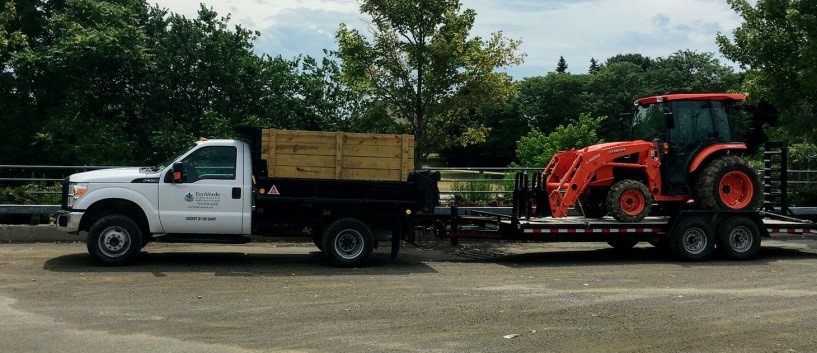
Our equipment is small so we can transport it to horse farms to collect their heavily bedded manure. We also believe small equipment is best for this site because it is better for navigating the fields and has a relatively low noise output.
We also have two larger horse stables that have third-party haulers who bring us their materials on roll-offs. One is a 15-yard dumpster; the other a 20-yard. They just come, dump, and leave about every two weeks.
Since starting the compost project, we average about 30 yards per week or about 1-1.5 loads of the truck pictured above per day (5-yard capacity). We might have days where four to six loads of our small truck might come in, but many days, no traffic at all comes in the gate.
Specialty Equipment
Compact Screener
We acquired a small, compact screener to screen out large rocks and clumps from the end product for specialty mixes that require a consistent, small particulate size.


Compact Grinder
We use this compact horizontal grinder to regrind certain wood chips and yard waste trimmings down to a more acceptable size for composting. This is used on a limited basis, and since it can be loud, we are restricting the hours of use to midday and only on weekdays.
John Deibel is an independent agricultural consultant on contract with EcoVerde to set up the site properly, oversee testing, and perform site management. John is also responsible for assisting the Carrs with the startup of their organic farm at the same time. John is a native of East Aurora and has worked many years in agronomy and agriculture across communities of all sizes with a primary focus on farmland retention and sustainability.